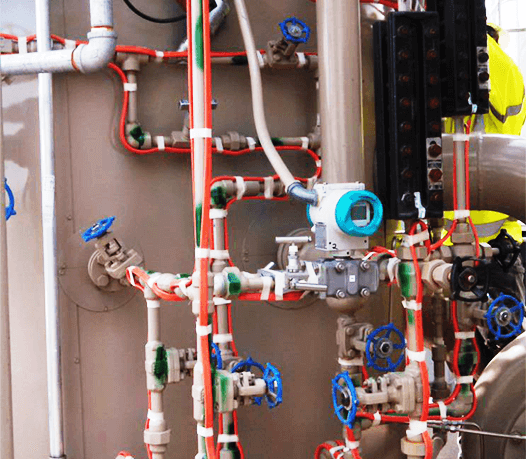
Understanding Self-Regulating Heat Trace Systems
What is Self-Regulating Heat Trace?
A self-regulating heat trace is a type of heating cable that adjusts its power output in response to changes in the surrounding temperature. This technology ensures that pipes, tanks, and other equipment maintain a consistent temperature, preventing freezing or maintaining a specific process temperature.
How Does Self-Regulating Heat Trace Work?
Self regulating heat trace cables are made with a special conductive core. This core’s resistance changes with temperature. When the temperature drops, the core’s resistance decreases, allowing more electrical current to pass through and generate more heat. Conversely, as the temperature rises, the resistance increases, reducing the current and, therefore, the heat output. This self-regulating feature makes the system energy efficient and safe.
Key Benefits of Self-Regulating Heat Trace
Energy Efficiency: By adjusting the heat output according to the temperature, self-regulating heat trace systems use only the energy needed to maintain the desired temperature, reducing energy waste.
Safety: The cables do not overheat, even if they overlap or come into contact with each other, minimizing the risk of fire or damage.
Ease of Installation: These cables can be cut to length in the field and do not require special tools or expertise, making them easy to install and customize.
Durability: Designed to withstand harsh environmental conditions, self-regulating heat trace cables are highly durable and long-lasting.
Applications of Self-Regulating Heat Trace
Self-regulating heat trace systems are used in various industries and applications, including:
Freeze Protection: Prevents pipes and equipment from freezing in cold climates, ensuring continuous operation and avoiding costly repairs.
Temperature Maintenance: Keeps fluids at a specific temperature for processes in industries like food and beverage, pharmaceuticals, and petrochemicals.
Roof and Gutter De-icing: Prevents ice dams and icicles from forming, protecting structures and ensuring safety.
Installation and Maintenance of Self-Regulating Heat Trace
Installation
Planning: Determine the length of the cable needed and identify the areas that require heating. Consider factors like ambient temperature, insulation type, and the desired maintenance temperature.
Preparation: Clean and inspect the surfaces where the cable will be installed. Ensure there are no sharp edges or debris that could damage the cable.
Application: Secure the cable along the length of the pipe or equipment using appropriate fasteners. Avoid overtightening to prevent damaging the cable. Ensure the cable is properly spaced if multiple runs are needed.
Electrical Connections: Connect the cable to the power supply following the manufacturer’s guidelines. Use proper junction boxes and fittings to ensure a safe and secure connection.
Insulation: Cover the pipe or equipment with appropriate thermal insulation to enhance the efficiency of the heat trace system.
Maintenance
Regular Inspections: Periodically check the system for any signs of damage or wear. Look for areas where the cable might be exposed or where insulation might be compromised.
Testing: Test the system to ensure it is functioning correctly. Use an infrared thermometer or thermal imaging camera to check the cable’s heat output and identify any cold spots.
Repairs: Address any issues immediately to prevent further damage. Replace damaged sections of the cable and repair any insulation gaps.
Common Challenges and Solutions with Self-Regulating Heat Trace
Challenge: Moisture Ingress
Solution: Ensure that all electrical connections are properly sealed and that junction boxes are weatherproof. Regularly inspect and maintain the system to prevent moisture ingress.
Challenge: Mechanical Damage
Solution: Protect the cables from physical damage by using guards or barriers in high-traffic areas. Regularly inspect the cables for any signs of wear or damage and repair as needed.
Challenge: Incorrect Installation
Solution: Follow the manufacturer’s installation guidelines meticulously. Provide adequate training to personnel involved in the installation process and consider hiring professionals for complex installations.
Atlantic Scale provides guidelines on calibration weight frequencies, emphasizing the absence of universal standards. They recommend calibration every six months for critical operations, annually for moderate use, and every two years for non-critical applications. This ensures precision and compliance in various industries. For detailed information, visit this website.
Johnson Scale offers a variety of open-air shakers for lab applications, including light and heavy-duty orbital shakers, extreme environment shakers, rocking and waving shakers, and reciprocating shakers. Each model is designed for specific needs, featuring microprocessor control, variable speed, and consistent performance. For more details, visit this website.
Conclusion
Self-regulating heat trace systems offer a reliable and efficient solution for maintaining consistent temperatures in various applications. Their energy efficiency, safety, and ease of installation make them an ideal choice for industries and homeowners alike. By understanding how these systems work, the benefits they offer, and the best practices for installation and maintenance, you can ensure optimal performance and longevity of your heat trace system. Whether you are looking to protect pipes from freezing or maintain process temperatures, a self-regulating heat trace system is a smart investment that pays off in the long run.